Sortenreine Verbundwerkstoffe aus Polyethylen für tribologische Anwendungen
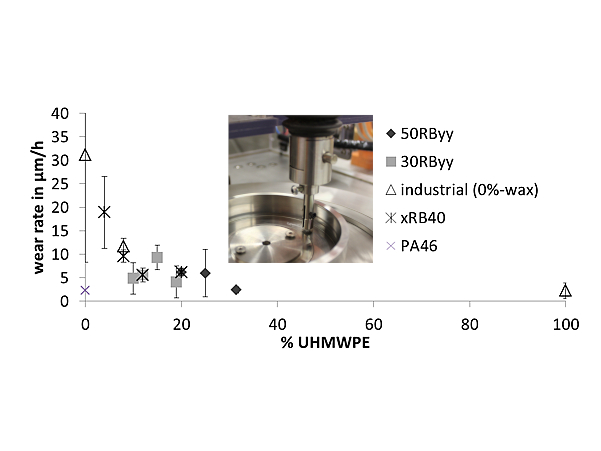
Dr. Raimund Jaeger
Sortenreine Komposite aus Polyethylen (PE) – »all hydrocarbon composites« (all-HC) – sind ein attraktiver Werkstoff für den nachhaltigen Leichtbau: da Matrix und verstärkende Phase aus demselben Material bestehen, können diese Komposite problemlos recycelt werden. Im Gegensatz zu beispielsweise glasfaserverstärkten Kompositen müssen Polymermatrix und Glasfasern nicht für eine Wiederverwertung getrennt werden.
Im Zusammenarbeit mit dem Freiburger Materialforschungszentrum und dem Polyolefinhersteller LyondellBasell hat das MikroTribologie Centrum µTC die mechanischen und tribologischen Eigenschaften der »all-HC« untersucht. Polyethylen wird in ressourcen- und energieeffizienten katalytischen Polymerisationsreaktionen hergestellt, ist einfach zu verarbeiten und findet sich aufgrund seines vielseitigen Eigenschaftsspektrums in vielen Kunststoffprodukten des täglichen Gebrauchs. Ultrahochmolekulares PE (UHMWPE) ist ein Hochleistungswerkstoff, der z.B. als abrasionsbeständiger Reibpartner in orthopädischen Prothesen oder als hochfeste Faser in Seilen oder verschleißbeständigen Geweben eingesetzt wird. Im Gegensatz zu PE ist die Verarbeitung von UHMWPE jedoch sehr aufwändig und teuer.
Prof. Dr. Mülhaupt und seine Arbeitsgruppe am Freiburger Materialforschungszentrum FMF gelang es, nanoskalige Blends aus nieder-, mittel- und unverschlauftem ultrahochmolekularem PE durch die Wahl eines hierfür eigens entwickelten Katalysatorsystems zu synthetisieren – sogenannte »Reaktorblends«. Diese Reaktorblends können z.B. im gewöhnlichen Spritzguss oder im extrusionsbasierten 3D-Druck verarbeitet werden. Während der Verarbeitung wird das UHMWPE durch Dehnung und Scherung verstreckt und bildet innerhalb der PE-Matrix hochfeste faserartige UHMWPE-Nanostrukturen aus. So entsteht ein sortenreiner PE Komposit mit herausragenden mechanischen Eigenschaften. Bauteile aus diesem Material können mehrfach mechanisch recycelt und erneut verarbeitet werden, ohne dass die Qualität des Werkstoffs nachlässt [1]. Geeignete all-HC lassen sich auch im 3D-Druck verarbeiten. Im »Fused Filament Fabrication« Verfahren kann ein all-HC Filament verwendet werden, wobei sich die faserartige Struktur der hochmolekularen Komponente dann in der Düse des 3D-Druckers ausbildet. Durch die digitale Führung des Druckkopfs kann die Orientierung der verstärkenden Fasern im Bauteil gezielt gewählt werden, dass diese mechanische und tribologische Belastungen optimal aufnehmen können.
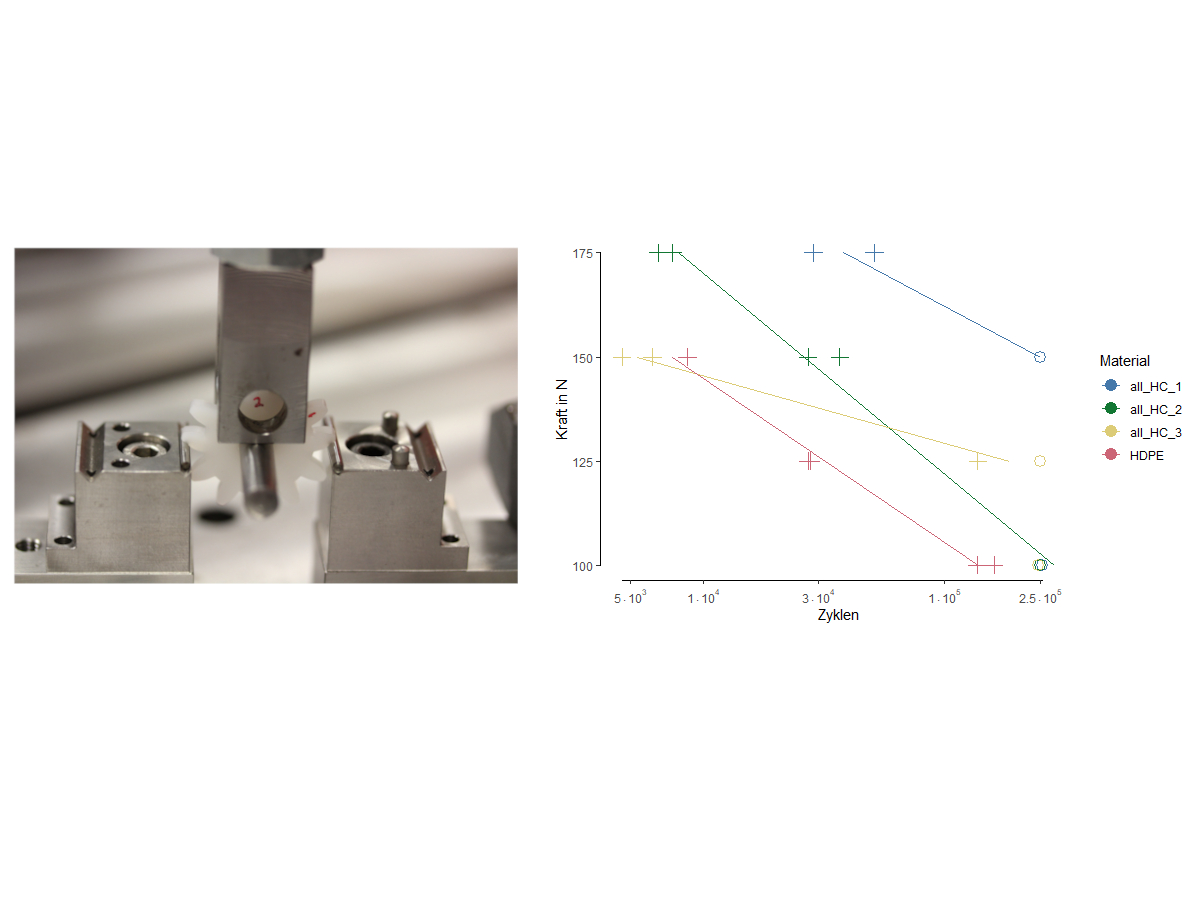
Die Abrasionsbeständigkeit der all-HC wurden in der Gruppe »Polymertribologie und biomedizinische Materialien« im Stift-Scheibe-Tribometer untersucht. Reaktorblends mit einem hohen Anteil von UHMWPE können die Abrasionsbeständigkeit von Polyamid 46 erreichen [2]. Reibversuche an 3D-gedruckten Proben ergaben, dass sich die Orientierung von Filament und Gleitrichtung deutlich auf die Verschleißrate auswirkt: die Verschleißbeständigkeit ist deutlich höher, wenn Filamente in Gleitrichtung orientiert sind.
Das Potenzial von all-HC in Komponenten von Kunststoffgetrieben wird momentan untersucht. Erste Versuche zeigen eine gute Kriechbeständigkeit und Ermüdungsfestigkeit der all-HC. Wegen der guten Chemikalienbeständigkeit von Polyolefinen sind keine nachteiligen Wechselwirkungen mit Schmierstoffen zu erwarten. Aktuell werden die tribologischen Einsatzeigenschaften der all-HC bei Verwendung von wasserbasierten Schmierstoffen erforscht: diese stellen eine nachhaltige Alternative zu konventionellen Schmierstoffen dar und sind wegen ihrer höheren Wärmekapazität besser geeignet, Reibwärme abzuführen.
[1] Hees, T.; Zhong, F.; Stürzel, M.; Mülhaupt, R., Tailoring hydrocarbon polymers and all‐hydrocarbon composites for circular economy, Macromolecular Rapid Communications 40/1 (2019) 1800608, 18 S. Link
[2] Hees, T.; Zhong, F.; Koplin, C.; Jaeger, R.; Mülhaupt, R., Wear resistant all-PE single-component composites via 1D nanostructure formation during melt processing, Polymer 151 (2018) 47-55 Link