Strukturoptimierte Systembeschichtung für die Abformung hochglänzender Kunststoffteile
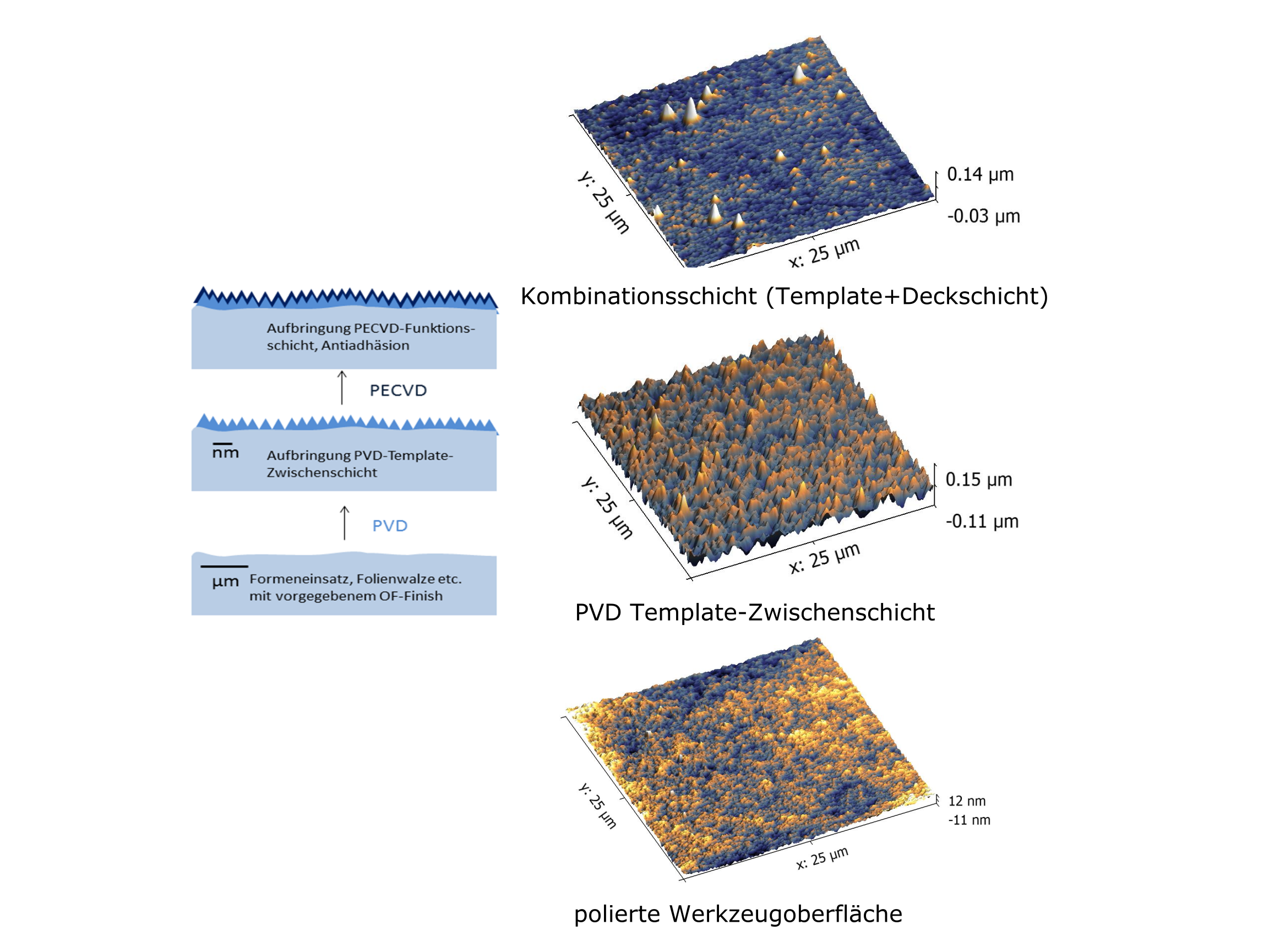
Verschleißfeste PVD/PECVD-Systembeschichtungen mit angepasster Oberflächentopografie ermöglichen prozesssicher Abformung von hochglanzpolierten Kunststoffformwerkzeugoberflächen
Zur Erzeugung von Kunststoffartikeln mit hochglänzenden Oberflächen werden hochganzpolierte Werkzeugoberflächen bei hohen Temperaturen in Kontakt mit polymeren Formmassen gebracht und dabei so gut wie möglich abgeformt. Der formschlüssige Kontakt zwischen Polymer und Werkzeug resultiert in einer sehr großen effektiven Kontaktfläche, an der sich van-der-Waals-artige Anziehungskräfte sowie chemische Wechselwirkungen ausbilden, die bei einer anschließenden Entformung wieder überwunden werden müssen. Dies kann speziell bei sehr glatten Werkzeugoberflächen soweit führen, dass eine prozesssichere Entformung nicht mehr gewährleistet werden kann.
Zur Lösung dieses Problems können zwei Ansätze verfolgt werden. Einerseits können durch eine chemische Veränderung der Werkzeugoberfläche oder durch Reduzierung der Kontaktfläche die Anziehungskräfte reduziert werden. Letzteres wird durch gezieltes mechanisches Aufrauen der Werkzeugoberfläche bewerkstelligt. So lassen sich Haftkräfte zwar oftmals reduzieren, die daraus resultierende, verminderte Oberflächengüte erlaubt allerdings nur eine Anwendung in Einzelfällen. Ähnlich verhält es sich bei der Aufbringung antiadhäsiver Beschichtungen. Zwar sind Beschichtungen mit möglichst niedriger Oberflächenenergie und geringem polaren Anteil (z.B. siliziumhaltige Beschichtungen auf DLC-Basis) in der Lage, Entformkräfte zu reduzieren, ihre Rauheit lässt sich aber nur schwer über den Beschichtungsprozess steuern, was zu einer ungewollten Aufrauhung der Formwerkzeugoberfläche führt.
Eine weitere Verbesserung kann daher nur erreicht werden, wenn durch eine Beschichtung sowohl die chemische Wechselwirkung, als auch die Kontaktfläche (Nanostruktur) optimiert wird. Für Hochglanzoberflächen ergibt sich daraus ein Spannungsfeld, in dem bisher die beiden Anforderungen nicht gleichzeitig erfüllt werden können.
Glatt ist nicht gleich glatt
Das MikroTribologie Centrum forscht deshalb an der Strukturaufklärung und der Optimierung der Kontaktfläche zwischen Polymer und Werkzeug in einem Skalenbereich, der stets im optischen Hochglanzbereich zu liegen kommt.
Als Hochglanzoberfläche werden im industriellen Umfeld Oberflächen mit einer mittleren Rauheit von Ra < 20nm, vorzugsweise Ra < 10 nm, definiert. Zur Aufklärung des Adhäsionsverhaltens ist eine exakte mathematische Beschreibung von Hochglanzoberflächen notwendig, die insbesondere die Wahl aussagekräftiger Kenngrößen erfordert. Die Forschungsarbeiten am MikroTribologie Centrum haben gezeigt, dass die Beschreibung von Hochglanzoberflächen und der Korrelation der Werkzeug-Oberflächentopografie mit den gemessenen Entformungskräften äußert komplex ist und die Angabe der in der EN-ISO 4288:1997 definierten Oberflächenrauwerte Ra oder Rq nicht ausreicht.
Für eine aussagekräftige Beschreibung der Oberfläche mussten sowohl Flächenrauheitsparameter (Sa, ISO 25178-3), Abstandsparameter (Spitzendichte, Sds) und Hybridparameter (Steilheit der Oberfläche, Sdq) als auch Verteilungsfunktionen (Höhenverteilung, Spitzenverteilung, Krümmung) sowie die in der Tribologie gebräuchlichen Abbot Firestone Curve (AFC) und die Power Spectral Density (PSD) ausgewertet werden. Die Korrelation der Oberflächenparameter (Sa, Sds, Sdq, AFC, PSD) mit den gemessenen Haftkräften hat z.B. gezeigt, dass neben der Rauheit (Sa) vor allem die Spitzendichte (Sds) einen signifikanten Einfluss auf die Haftkräfte hat.
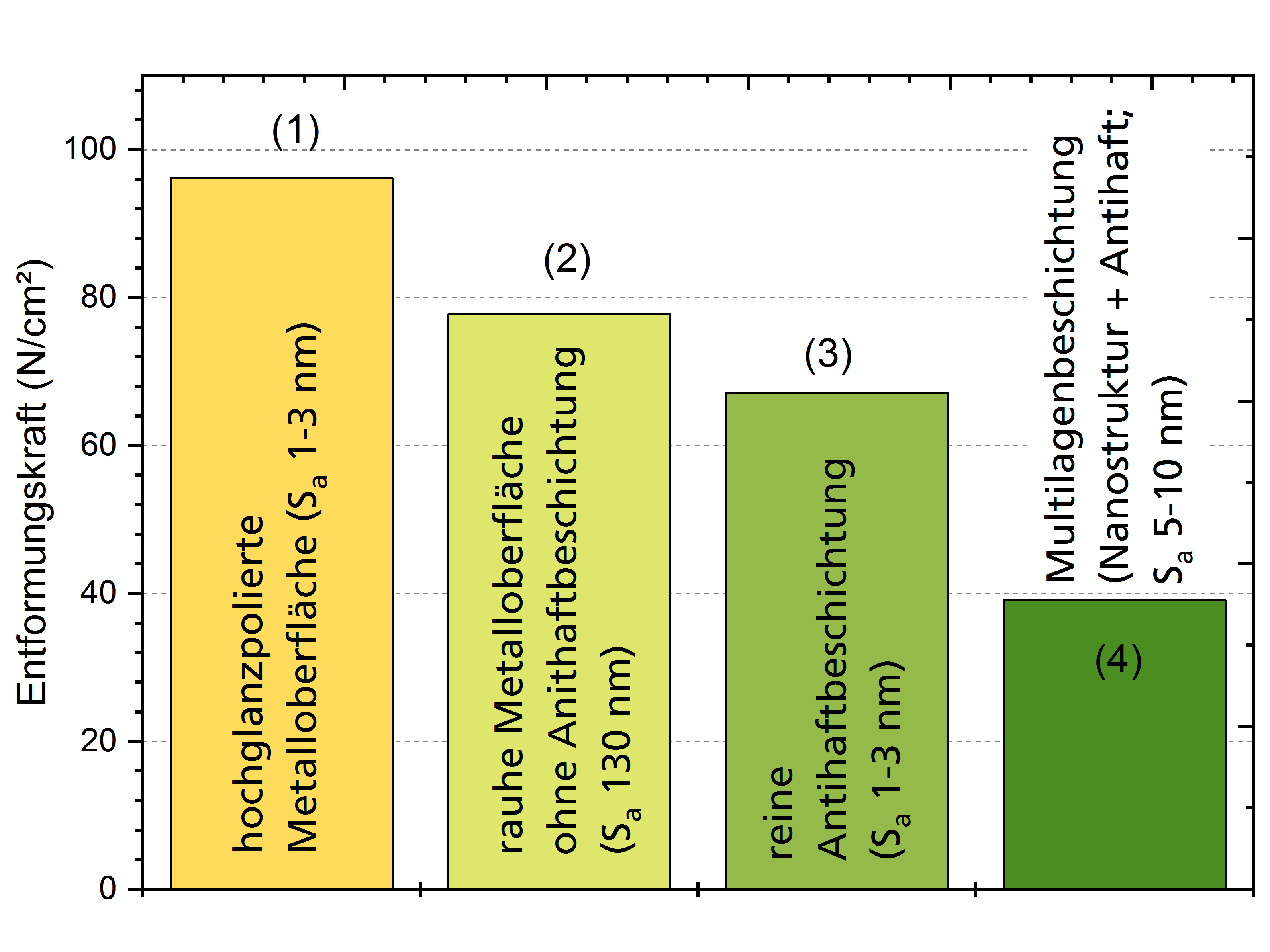
Die Kombination macht’s
Um den Widerspruch zwischen Hochganzabformung und Kontaktflächenminimierung zu überwinden, entwickelt das MikroTribologie Centrum in Zusammenarbeit mit dem Fraunhofer IST und dem Fraunhofer LBF ein mehrlagiges Schichtsystem, das aus einer nanostrukturierten PVD-Hartstoff-Templateschicht und einer antiadhäsiven Deckschicht besteht.
Durch gezielte Steuerung der Abscheideparameter Druck, Leistung und Sputterzeit gelang es, die Oberflächentopographie der Kombinationsschicht bezüglich der Parameter Rauheit (Sa = 1 nm - 20 nm), Spitzendichte (Sds 1μm-1 - 5 μm-1) und mittlerer Oberflächensteilheit (Sdq 1° - 10°) in den o.g. Grenzen gezielt so einzustellen, dass eine Aufrauhung der Oberfläche und damit die Reduktion der Kontaktfläche nur auf einer Längenskala stattfanden, die den optischen Hochglanzeindruck erhielten.
Durch diese PVD/PECVD-Kombinationsbeschichtung ist es gelungen, die Ablösekräfte in Heißprägeprozessen für PET gegenüber einer unbehandelten Werkzeugoberfläche, um ca. 60% zu reduzieren. Ohne eine Strukturoptimierung, d.h. nur mit einer antiadhäsiven Deckschicht, konnten die Kräfte nur um ca. 40% reduziert werden. Die Rauheit der abgeformten Teile wurde durch die mehrlagige Beschichtung zwar von einem Sa von 3,3 nm auf 7,5 nm erhöht, liegt jedoch immer noch deutlich innerhalb des als Hochglanz definierten Bereichs. Der optische Eindruck wurde durch diese Veränderung nicht nennenswert gemindert.
Dank
Die Arbeiten wurden durch ein IGF-Vorhaben (Nr. 19545 N) der Forschungsvereinigung Forschungsgesellschaft Kunststoffe e. V. (FGK), Haardtring 100, 64295 Darmstadt über die AiF im Rahmen des Programms zur Förderung der industriellen Gemeinschaftsforschung und -entwicklung (IGF) vom Bundesministerium für Wirtschaft und Energie aufgrund eines Beschlusses des Deutschen Bundestages gefördert.
Dr. Frank Meyer,
Dr. Frank Burmeister,
Dr. Bernd Steinhoff, Abteilung Kunststoffverarbeitung und Bauteilauslegung des Fraunhofer-Institut für Betriebsfestigkeit und Systemzuverlässigkeit (LBF)
Dr. Hans Kothe, Arbeitsgruppe Thermoplastverarbeitung Bereich Kunststoffe der Fraunhofer-Institut für Betriebsfestigkeit und Systemzuverlässigkeit LBF
Dr.-Ing. Martin Keunecke, Leiter der Arbeitsgruppe Tribologische Systeme am Fraunhofer-Institut für Schicht- und Oberflächentechnik IST