Modernes und vielseitiges Beschichtungszentrum
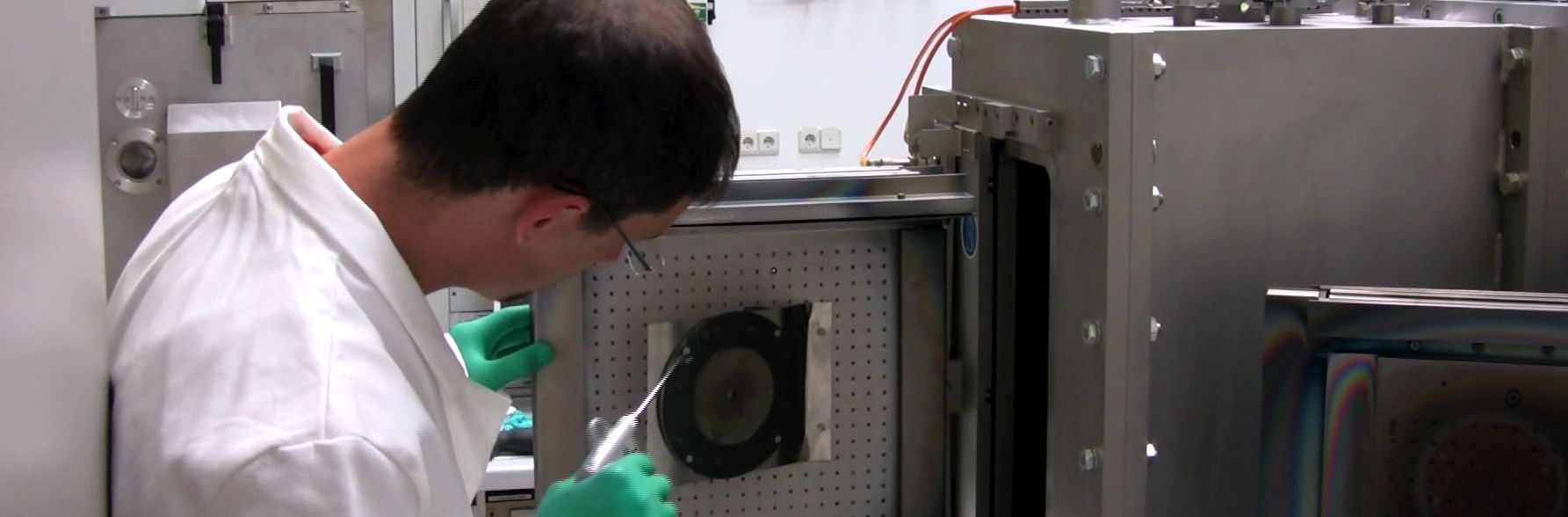
Dr. Frank Burmeister, Bernhard Blug
Durch den Zusammenschluss der beiden Bereiche »Tribologische Beschichtungen« und »Funktionale Schichtmaterialien« ist am Standort Freiburg ein modernes Beschichtungszentrum mit vielfältigen Möglichkeiten zur Erforschung tribologischer Fragestellungen und Entwicklung innovativer Schichtsysteme entstanden. Die vorhandenen Abscheidetechnologien umfassen dabei sowohl das industriell weit verbreitete, klassische Magnetronsputtern im reaktiven HF-, DC- und DC-Puls-Mode, Ionenstrahlprozesse, Plasmapolymerisation als auch die plasmaassistierte Gasphasenabscheidung (PA-CVD). Dadurch können erstmalig die Stärken der verschiedenen Technologien vorteilhaft miteinander kombiniert werden. So weisen z.B. diamantähnliche Kohlenstoffbeschichtungen (DLC) für viele tribologische Anwendungen gute Verschleißfestigkeiten und niedrige Reibwerte auf. In wässrigen Medien bei höheren Temperaturen kommt es aber oftmals zu Spannungsrisskorrosion. Zudem weisen DLC-Schichten unter hohen Temperaturen wegen ihres geringen Wärmeausdehnungskoeffizienten auf metallischen Substraten mit hohen Ausdehnungskoeffizienten Haftungsprobleme auf. Durch das Aufsputtern einer angepassten Hartstoffschicht als Kompatibilisierungsschicht lassen sich jedoch die o.g. Schwierigkeiten umgehen und die Standzeiten von DLC-Beschichtungen z.B. für von Dichtungen und Gleitlagern in wässrigen Umgebungen signifikant erhöhen. Auch können so z.B. überrollfeste Wasserstoffbarriereschichten zur Verhinderung von sogenannten »White Etching Cracks« für Lageranwendungen abgeschieden werden. Umgekehrt eröffnet die Abscheidung schnell wachsender, elektrisch isolierender DLC-Beschichtungen auf metallischen Komponenten neue Möglichkeiten im Bereich der Dünnschichtsensorik. So können z.B. erstmals über Dünnschicht-Thermoelemente die Temperaturen auf der Oberfläche von Formwerkzeugen im Spritzgießprozess lokal und verzögerungsfrei erfasst werden, indem vor der Deposition der metallischen Ni/NiCr-Leiterbahnen eine Isolationsschicht im PECVD-Verfahren auf die Werkzeugoberfläche aufgebracht wird.
In den Sputteranlagen können je nach Erfordernissen Substrate bis max. (300 cm)² bei Temperaturen bis max. 1000°C beschichtet werden. Als Anwendungen zu nennen sind u.a. thermomechanisch stabile Korrosions- und Antiadhäsivbeschichtungen für Formenwerkzeuge für die Glas- und Kunststoffformgebung. Auch anspruchsvolle Aufgabenstellungen wie die heteroepitaktische Abscheidung einkristalliner Iridiumschichten für die Erzeugung von electronic-grade Diamantwafern wurden mit der vorhandenen Anlagentechnik bereits erfolgreich realisiert.
Im Bereich der PECVD-Beschichtungen stehen Anwendungen für den Verschleißschutz und die Lagertechnik im Vordergrund. Alleinstellungsmerkmale sind höchste Ebenheiten und Schichthomogenitäten auch über große Flächen sowie ein Hochrate-Abscheideprozess für DLC-Schichten, der Abscheideraten bis 10 µm/h bei Härten von 3000 HV und 60 µm/h bei 1200 HV erlaubt. Da die Anlagen größtenteils im Eigenbau hergestellt worden sind, können die lokalen Plasma- und Schichtabscheidebedingungen individuell auf kundenspezifische Bauteile angepasst und die geforderten Schichteigenschaften so optimiert werden. Auch der Aufbau von kundenspezifischen Anlagenkonzepten und Konfigurationen ist möglich.
Neben der eigentlichen Beschichtungstechnik steht auch eine umfangreiche Schichtanalytik zur Verfügung, die von mikrostrukturellen und chemischen Charakterisierungsmethoden bis hin zur Bestimmung wichtiger tribologischer Kennwerte (Härte, Reibwerte, Überrollfestigkeit etc.) reicht.
Durch die Konzentrierung der bisher über mehrere Gruppen verteilten Kompetenzen und apparativen Ausstattungen zu Schicht- und Oberflächentechnologien können nun anspruchsvolle Forschungsprojekte noch effizienter realisiert als auch schwierige Kundenanfragen zielgerichteter und erfolgreicher adressiert werden.