Abrieb von Elastomeren
Dr. Raimund Jaeger
Die Lebensdauer von Elastomerbauteilen wird häufig durch deren Abriebbeständigkeit bestimmt: So müssen Reifen gewechselt werden, wenn das Profil abgefahren ist, und Transportbänder verschleißen im Kontakt mit Führungen und Abstreifern. Eine abschließende Bewertung der Abriebbeständigkeit eines Bauteils kann häufig nur durch aufwändige Praxistests erbracht werden, beispielsweise indem man neu entwickelte Reifen auf der Straße testet. Während der Materialentwicklung ist es jedoch wünschenswert, erste Aussagen zum Abriebverhalten anhand von kleinen Proben und beschleunigten Messverfahren zu erhalten.
Verschleiß von Elastomeren durch Ermüdungsrisswachstum
Verschiedene Mechanismen werden als Ursachen des Verschleißes von Elastomeren diskutiert. Verschleiß kann durch eine hohe lokale mechanische Belastung verursacht werden, beispielsweise wenn aus dem Reifen eines Geländefahrzeugs ein Fragment nach dem Kontakt mit einer scharfen Kante herausgelöst wird. Im Gegensatz hierzu erfährt die Lauffläche eines rollenden Reifens durch den auftretenden Schlupf eine moderate Ermüdungsbelastung, die Ermüdungsrisse verursacht, welche wiederum zum Ablösen von Partikeln und somit zu Verschleiß führt. Neben den mechanischen Belastungen können (tribo)chemische Effekte - zum Beispiel die Degradation des Elastomers durch Ozon - zu Verschleiß führen.
Da der Verschleiß eines rollenden Reifens wesentlich durch den Ermüdungsverschleiß geprägt ist, wurde eine Modifikation des Klingenabrasiontests entwickelt, der als Methode zur Untersuchung des Abriebs durch Ermüdung etabliert ist. Im Klingenabrasionstest überstreicht eine scharfe Klinge die Elastomeroberfläche. Hierdurch entstehen auf der Oberfläche Riefen, die senkrecht zur Gleitrichtung der Klinge verlaufen. Durch das wiederholte Überstreichen dieser Strukturen erfährt die Riefenstruktur eine Ermüdungsbelastung, die zur Ausbildung von Ermüdungsrissen und zum Ablösen von Partikeln führt, also einen Verschleiß der Oberfläche zur Folge hat.
Wir haben die Klinge durch drei starr montierte Stahlkugeln ersetzt, die in einer kreisförmigen Spur über die Elastomeroberfläche gleiten (siehe Abb. 1). Diese Belastungsanordnung erzeugt ebenfalls eine Riefenstruktur und Materialabrieb durch Ermüdungsrisse. Die Spannungssituation, die durch den Kontakt mit den Kugeln in der Elastomerprobe entsteht, lässt sich jedoch im Gegensatz zum Kontakt mit einer Klinge definierter einstellen und besser durch Finite-Elemente-Simulationen analysieren.
Ein Tribometer für die Abriebmessungen ist in Abb. 2 dargestellt. Als Proben dienen flache Elastomerplatten der Abmessung 40 × 40 × 2 mm3. Die Pressung zwischen Kugeln und Probenoberfläche wird durch Totgewichte aufgebracht, die den Reibpartner von oben gegen die rotierende Probe drückt. Der Abrieb wird nach definierten Umdrehungszahlen durch Wägung ermittelt. Während der Messungen kann das Reibmoment über einen Drehmomentsensor und die vertikale Position des Reibpartners durch einen Taster ermittelt werden.
Messungen an Reifencompunds
Abbildung 3 zeigt die Zunahme des kumulativen Abriebs in Abhängigkeit der Anzahl der Umdrehungen für verschiedene Elastomercompounds. Im Allgemeinen wird ein linearer Anstieg des kumulativen Abriebs mit zunehmender Anzahl der Umdrehungen (d.h. mit Zunahme des Reibwegs bzw. der Anzahl der Wechselbelastungen) beobachtet. Die Steigung der Ausgleichgeraden entspricht der Verschleißrate im „eingelaufenen Zustand“, da sie Einlaufvorgänge - ein anfänglich höherer oder niedrigerer Masseverlust, der durch den y-Achsenabschnitt der Regressionsgeraden beschrieben wird - nicht berücksichtigt.
In den Abriebversuchen werden die Unterschiede zwischen den optimierten Reifencompounds (»NR-Lauffläche« und »BISYKA-Lauffläche«) und den nicht-optimierten Entwicklungsmustern (»SVR-10«, »PIP-90«, »Ski-3« und »NATSYN«) deutlich sichtbar. Der im Vergleich zu den optimierten Reifencompounds höhere Abrieb der nicht- optimierten Entwicklungsmuster ist so zu erwarten.
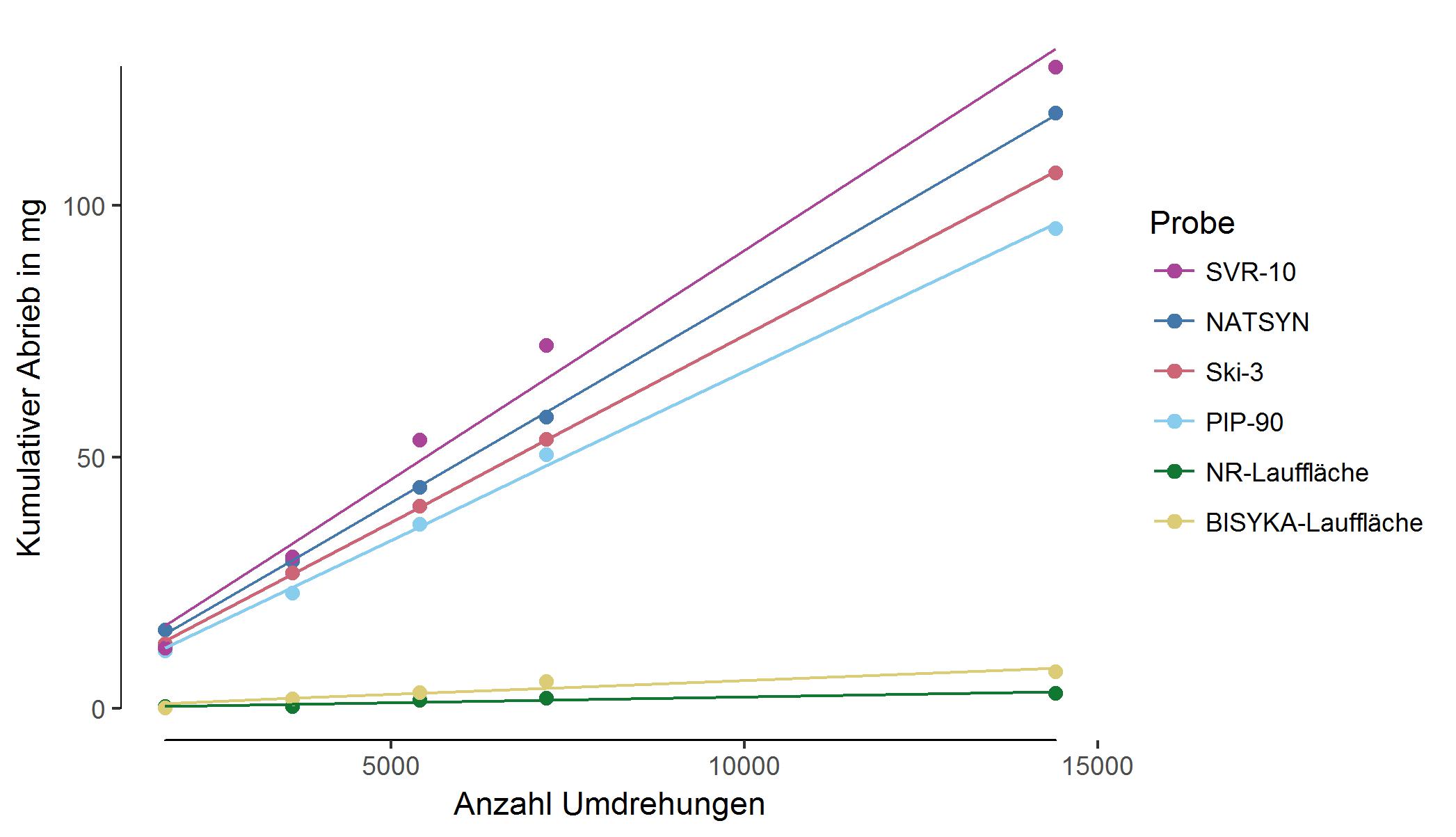
Für eine Bewertung der Ergebnisse der Abriebversuche sollte die reale tribologische Belastungssituation eines Reifens mit der tribologischen Belastung der Proben im Experiment verglichen werden. Messungen an einer Elastomermischung, die für Laufflächen von LKW-Reifen verwendet wird, ergaben, dass der Abrieb im Tribometer circa um einen Faktor 10 geringer ist als der Abrieb, den man im Betrieb erwarten würde. Ein plausibles Ergebnis, berücksichtigt man, dass der erhöhte Abrieb, der durch das Beschleunigen, Bremsen oder Kurvenfahrten und durch abrasive Belastungen, die z.B. durch raue Fahrbahnoberflächen entstehen, in dieser experimentellen Anordnung nicht abgebildet werden.